MoparInsiders Tours The Simpson Racing Factory:
We Get To See How Some Of The Most Popular Motorsports Safety Equipment Is Made...
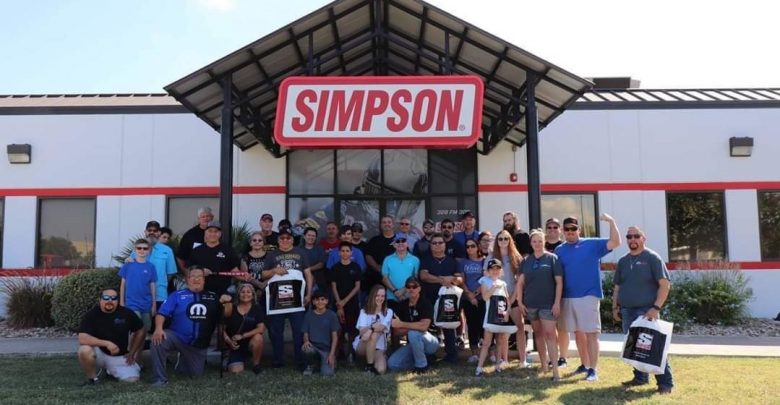
MoparInsiders was recently invited to join the Alamo City LX Modern Mopar Club on a tour of Simpson Racing’s facility in New Braunfels, Texas. As many of you may already know, Simpson Racing is a producer of safety equipment and their 80,000 sq.-ft facility, produces parachutes, seat belts, Hans devices, and helmets for a vast number of motorsports. Additionally, there is a full retail store on-site, to purchase all of their various products.
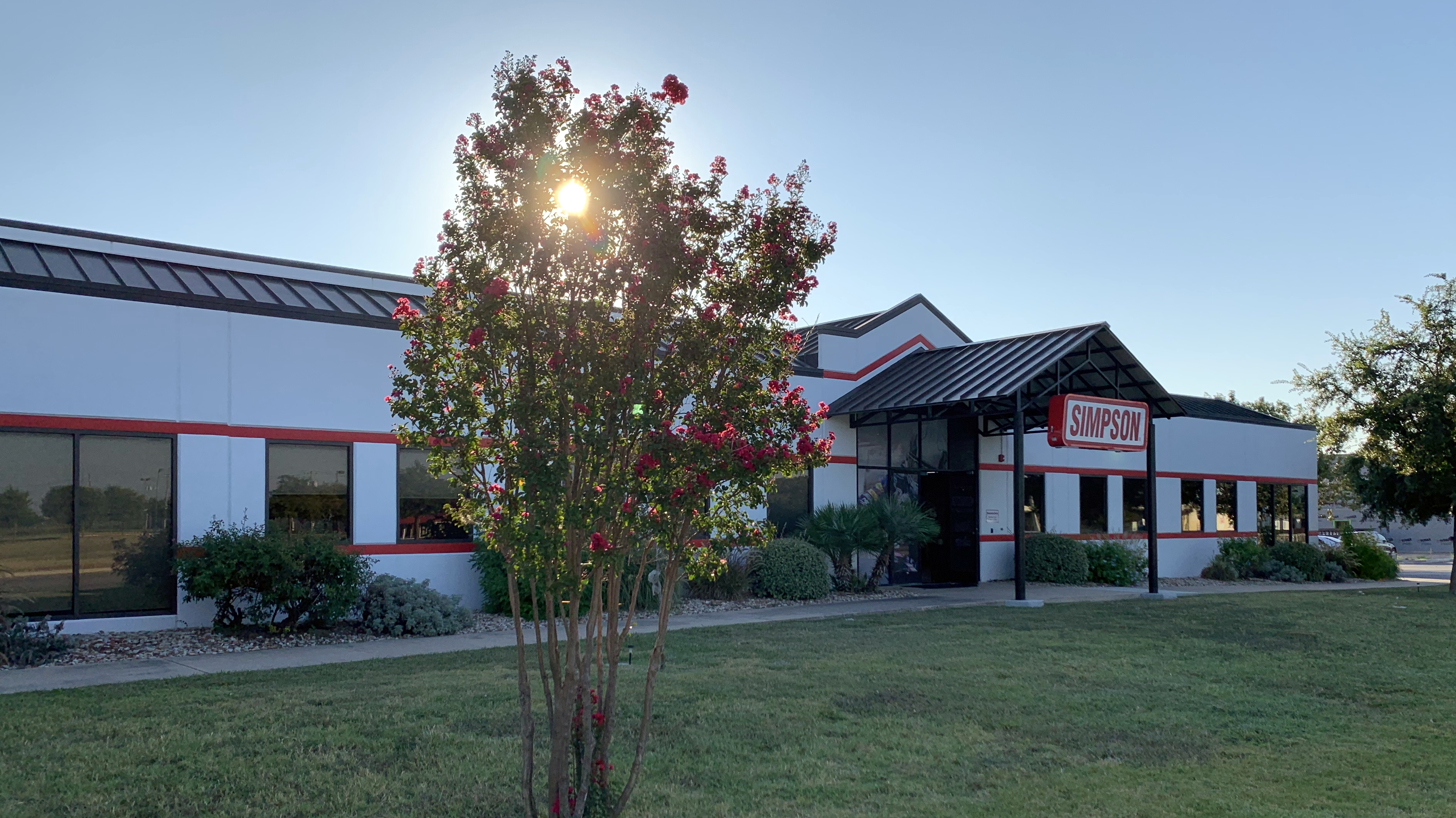
The tour began with a meet and greet before we made our way back to the sewing stations. At these sewing stations are where parachutes for drag racing are hand sewn. The parachutes can be ordered in either a stock color combination or various custom orders. Next rolls of 2-inch or 3-inch webbing are sewn to produce five, six, and seven-point harnesses for racing and aviation applications.
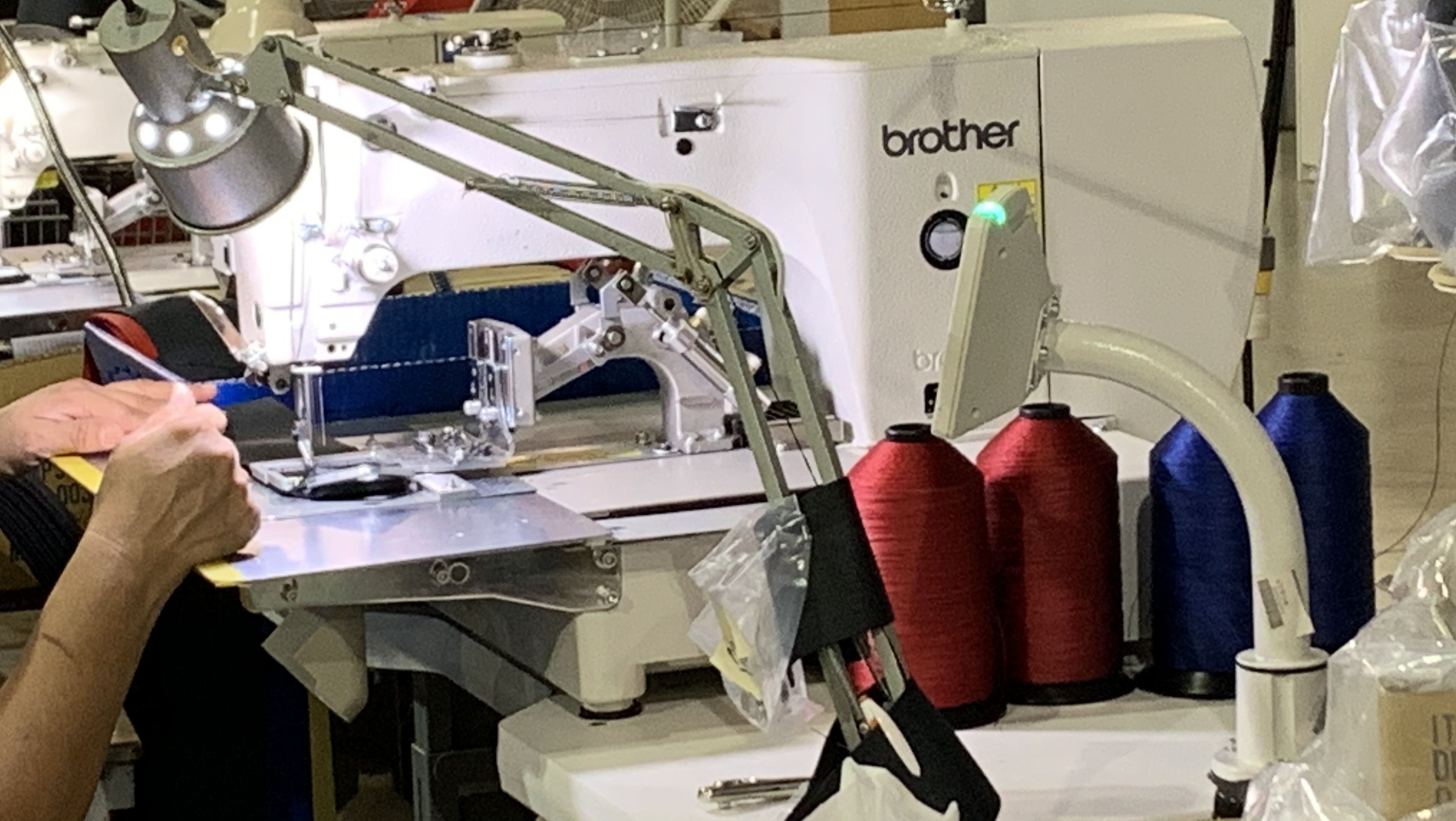
The next area we toured was the assembly area for head and neck restraints. All Hans devices are assembled here. The composite or carbon fiber components are supplied by a vendor and then all the components are put together, inspected, and boxed up for shipment. While in this area, we had the opportunity to compare one of the original Hans devices to the current generation of the device. It was amazing to see how this life-saving device has evolved over the year.
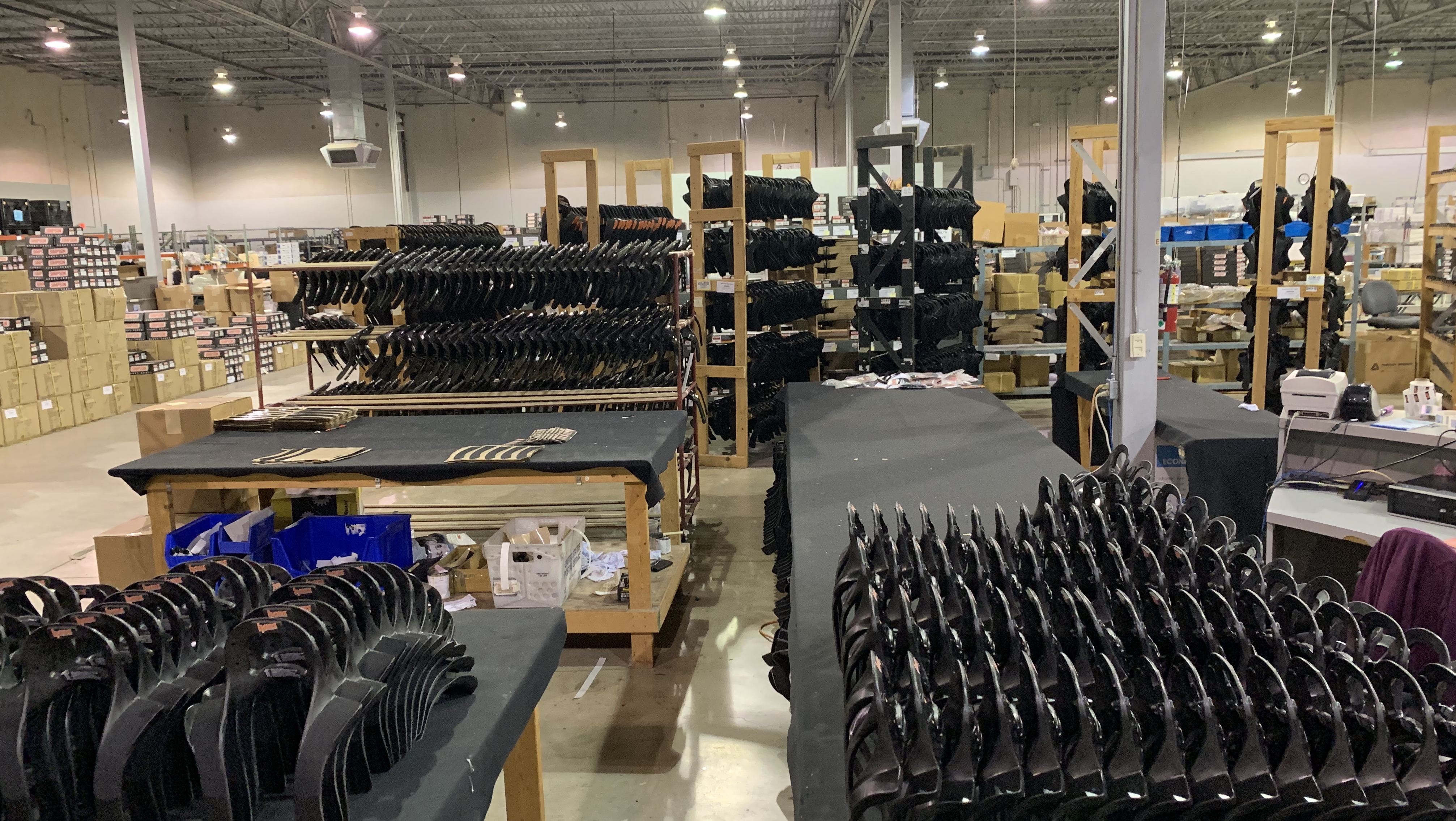
Next up was the helmets. The composite outer shells of the helmets are produced by laying woven mat and resin inside molds. The process is similar to fiberglass production, but Simpson does use a product-specific woven material. Once removed from the mold, the shell moves on to the paint shop where “stock” colors such as gloss black, matte black, red, white, blue or silver and applied to the shell. For an additional charge, Simpson can paint the shell in a custom color or even send the shell to a customer’s preferred painter for custom paintwork. Once the painting is complete, the shells join with the carbon fiber shells that are produced by a vendor for the final assembly process.
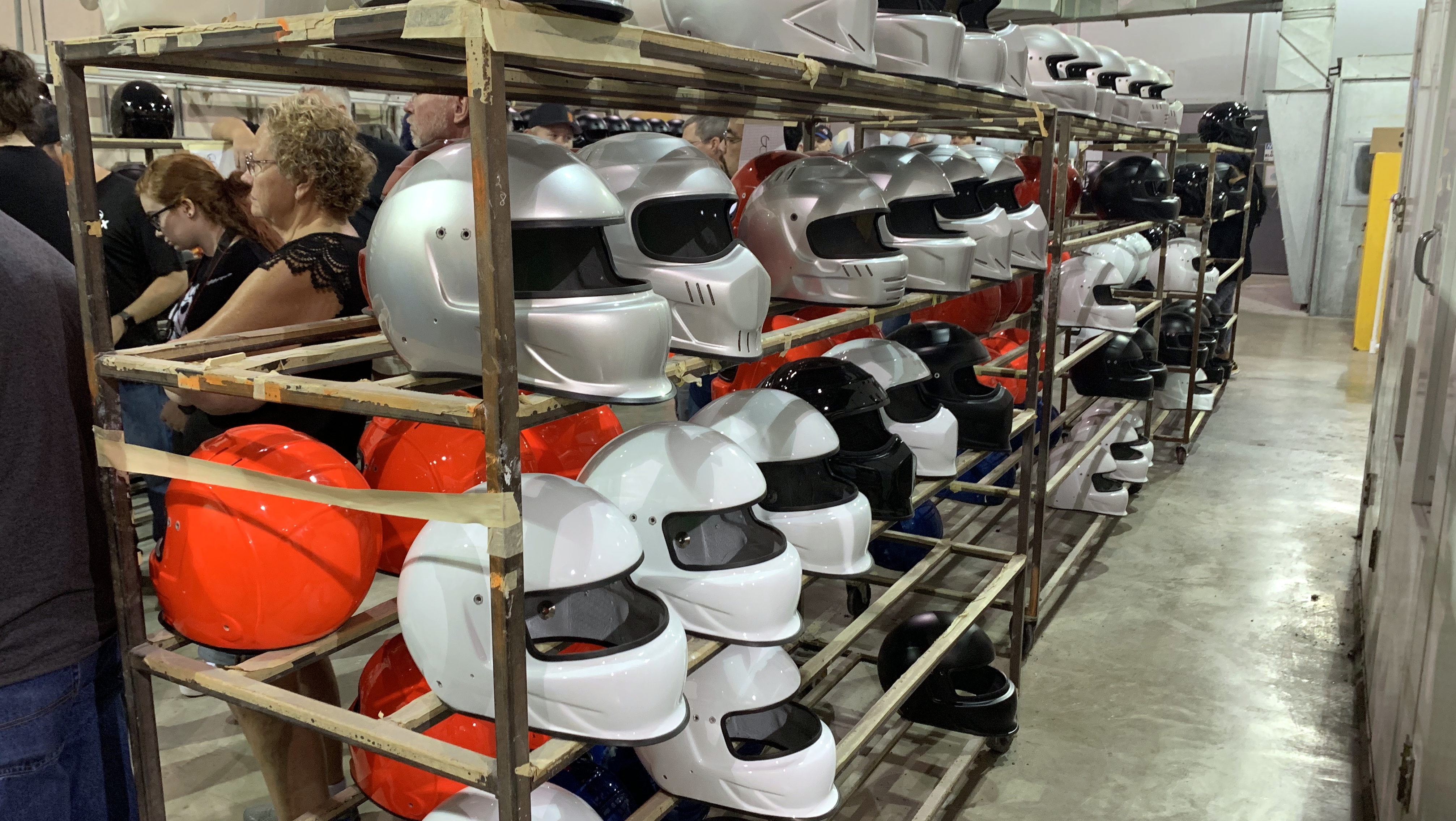
The key to the helmet is the foam and padding inside of it. Each style of helmet has a specific foam and padding mix to meet SFI specifications. New designs can even be tested on-site as part of the development process. Simpson Racing also offers inspection, repairs, recertification of harnesses, as well as Hans devices on-site.

Overall, it was a great tour and our group of roughly 35 people really enjoyed the opportunity to walk through the facility. We concluded the day with an opportunity to buy some great products in their retail shop along with group pictures outside. MoparInsiders would like to thanks Simpson Racing and our friends at the Alamo City LX Modern Mopar Club for the opportunity to check out the facility and see the great “Made in the USA” safety equipment being produced there.
Simpson Racing Factory Image Gallery: