VIDEO: An In-Depth Look Inside The New Detroit Assembly Complex – Mack Facility:
Take A Tour Inside The Home Of The New Jeep® Grand Cherokee L...
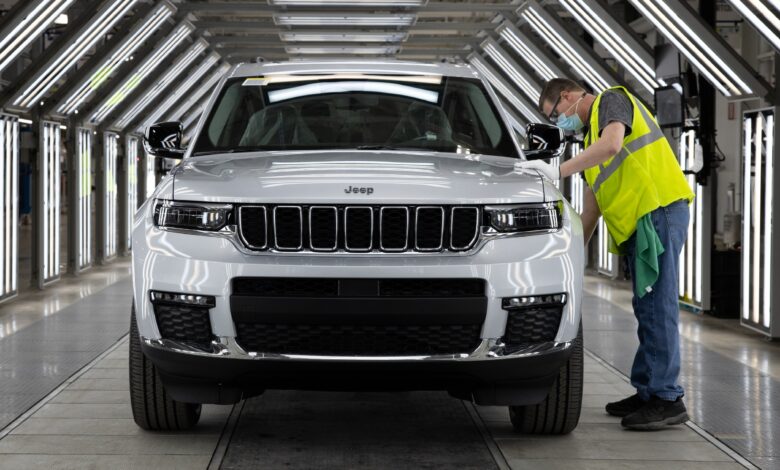
In February of 2019, Fiat Chrysler Automobiles (FCA) announced its plans to invest $1.6 billion to convert two of its smaller engine plants into a state-of-the-art assembly facility for its next-generation Jeep® Grand Cherokee (WL). The new assembly complex was part of a $4.5 billion investment that impacted five existing facilities in Michigan and aimed at creating 6,500 new jobs for the area.
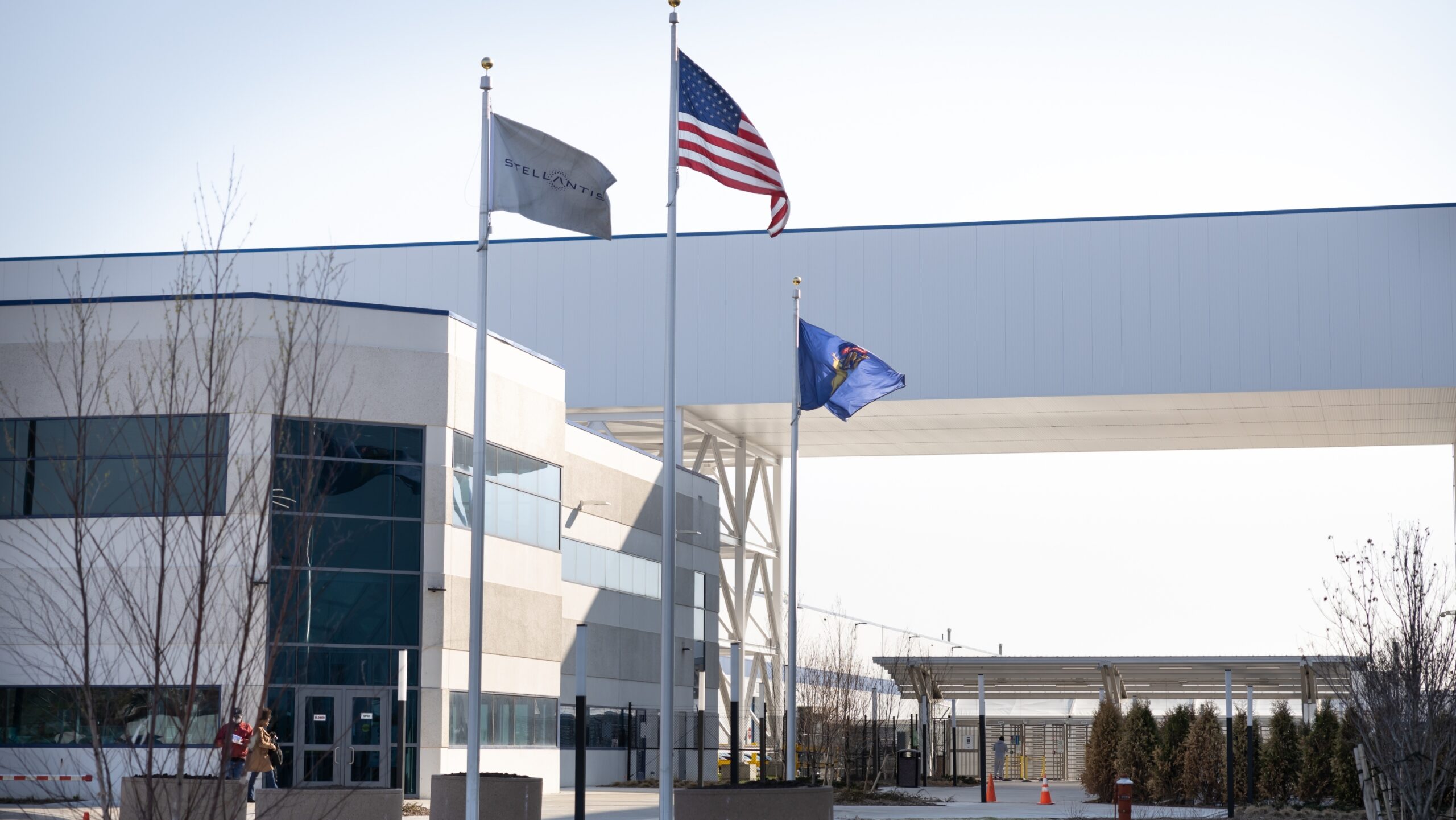
While we got a sneak peek at the work behind the scenes at the new Detroit Assembly Complex – Mack, the first new automotive assembly plant in the city of Detroit in 30 years, the new plant is now operational and cranking out all-new 2021 Jeep Grand Cherokee L. The Grand Cherokee L is the first variant of the new fifth-generation Grand Cherokee to hit the market and is the first three-row offering on the most awarded SUV nameplate in history.
Stellantis, the newly formed identity between the merger of Peugeot S.A. (PSA) and FCA, is giving us an in-depth tour of its newest assembly plant in action.
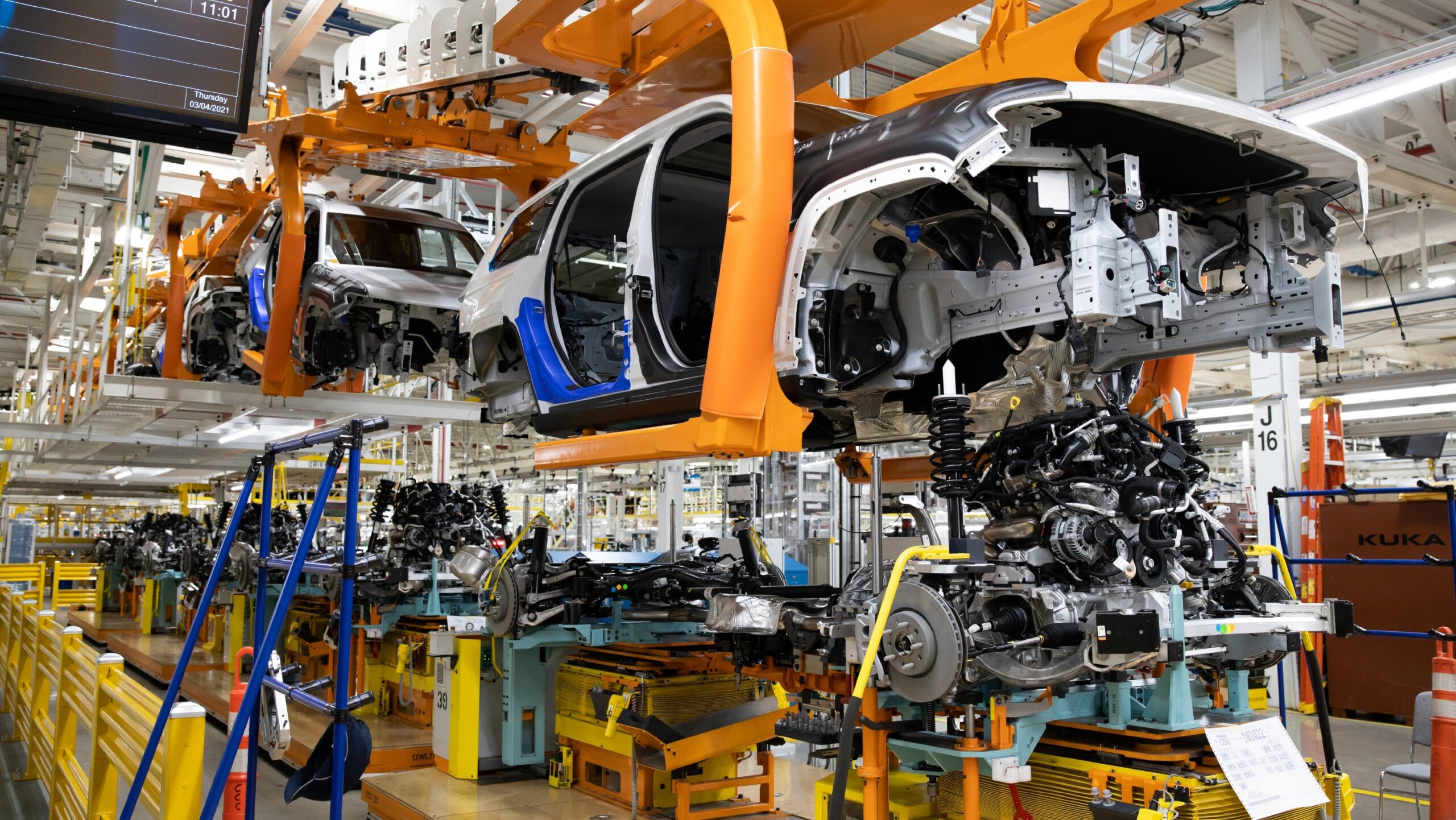
With over 100 years of manufacturing done on the site, the new Detroit Assembly Complex – Mack facility started construction in the second quarter of 2019 and was complete in less than two years with an ongoing pandemic. The Mack facility is 3 million square feet of floor space on 266 acres of property. The plant is made up of three main production facilities (body shop, paint shop, and general assembly).
With a workforce of 4,900 people, the Mack facility has 2,100 Detroiters filling positions within the complex. Employees work three shifts, five days per week at the current moment to fulfill the demand of the new 2021 Jeep Grand Cherokee.
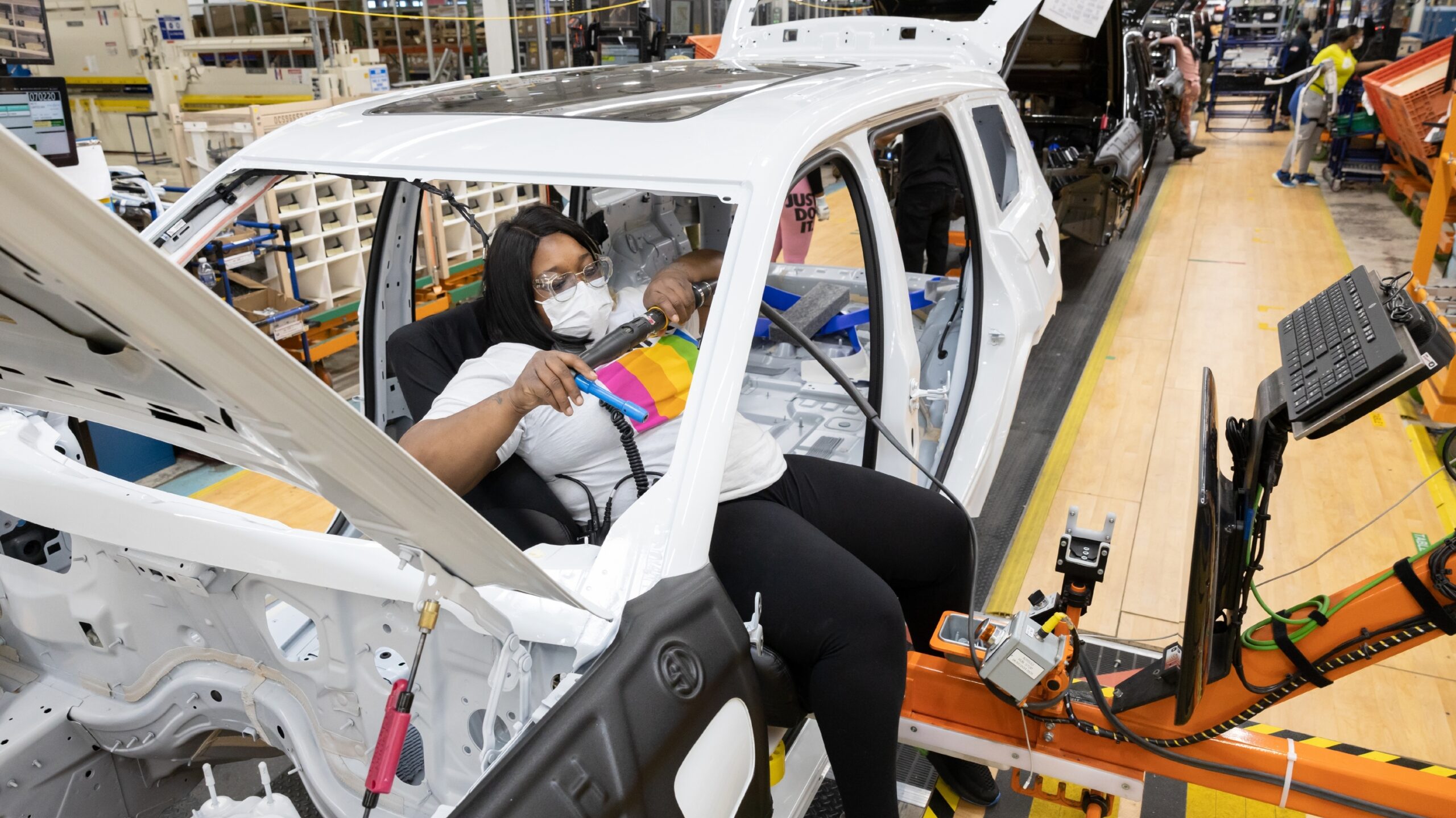
According to Stellantis, the new plant has 770 inbound trucks per day, as well as 76 trucks and 95 railcars outbound per production day. It takes 36 hours from start to finish to build a new 2021 Jeep Grand Cherokee L.
Body Shop:
The Mack facility’s 650,000 square-foot body shop is made up of the former Mack Engine II plant, which was idled in 2012. The Mack Engine II plant was completed in 2000 and produced it produced the 3.7-liter V6 engine for the Dodge Ram 1500, Dodge Dakota, Dodge Nitro, Jeep Liberty (Cherokee), Jeep Grand Cherokee, and Jeep Commander.

Now, the facility houses 578 robots that can produce a body of a Grand Cherokee L and make sure it fits perfectly together in about 2 hours.
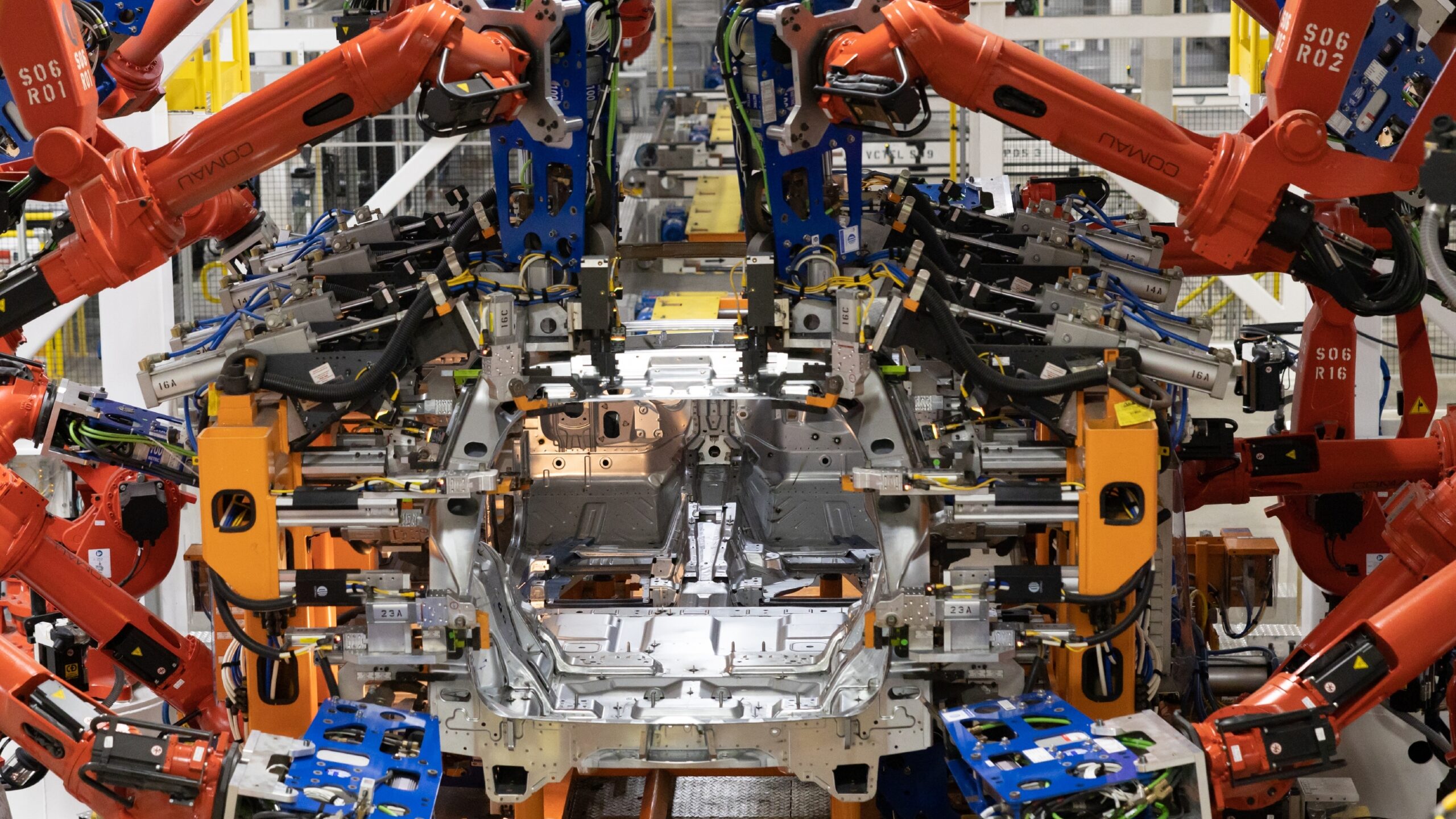
A net form is created for the Jeep Grand Cherokee L to establish the perfect dimensional environment to hang panels, such as the hood, liftgate, doors, and fenders before the body is pierced. Robots measure the gaps and fit to ensure they are symmetrical. There are 26 robots in the cell.
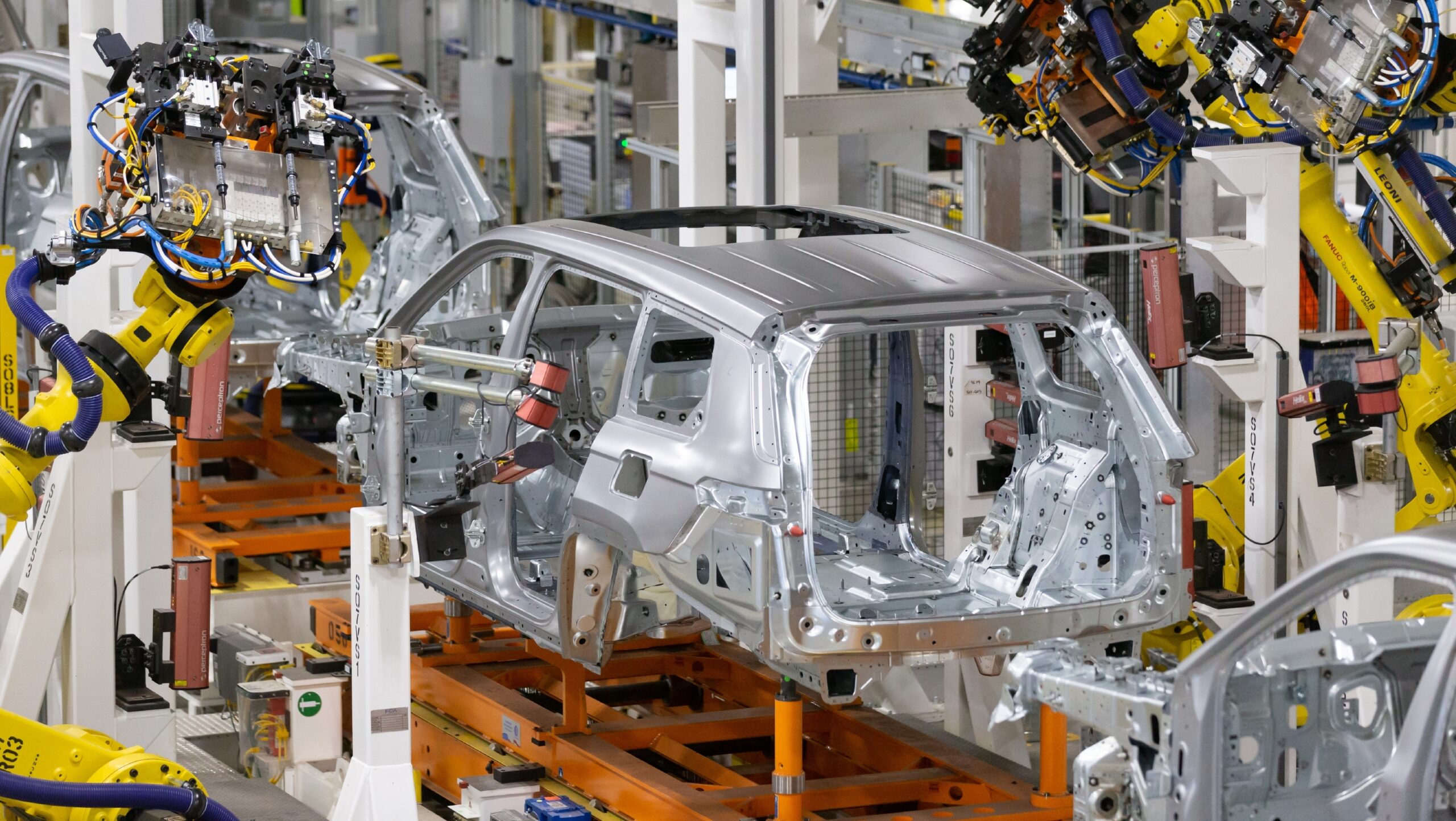
Radar technology is mounted on robots to measure hundreds of preprogrammed surface and alignment points to verify the build process. This 45-minute validation test is performed on a select number of vehicles across all three production shifts and complements the inline measurement system that measures every Jeep Grand Cherokee L coming through the body shop.
Paint Shop:
An all-new paint shop was build for the new Detroit Assembly Complex – Mack facility. The body shop measures 800,000 square feet and features five floors of space. It houses 124 robots that are fully automated thanks to a 100% robotic spray application, guaranteeing a perfect paint job every time.
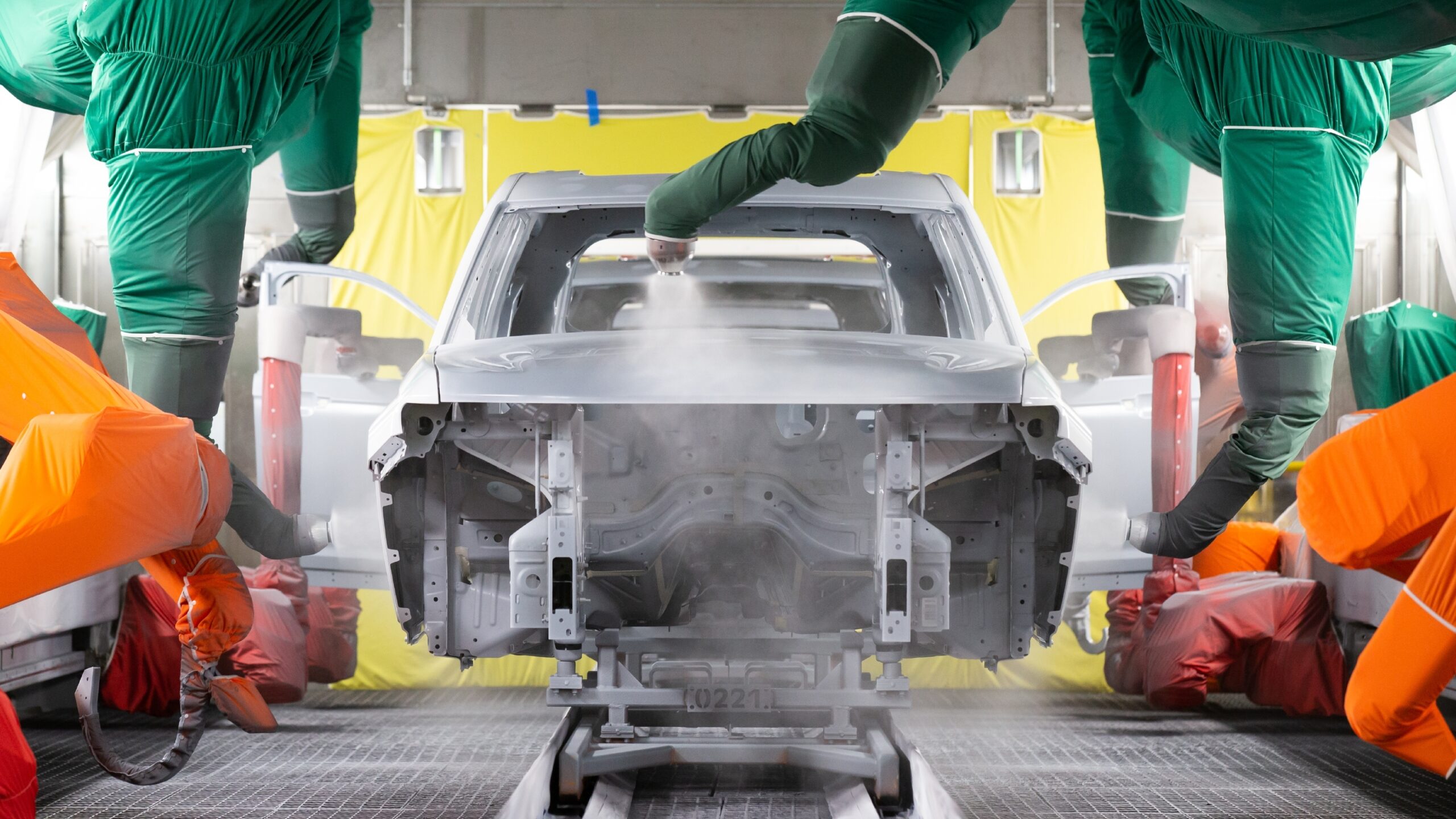
The 6 part process takes a total of 12 hours and the body shop can produce 11 different colors for the Grand Cherokee. The 6 part process includes the following steps…
- Phosphate E-Coat: Each vehicle goes through an E-Coat bath, giving the vehicle its first layer of corrosion protection
- Sealer: 28 robots apply 208 feet of sealer in each Grand Cherokee L to prevent leaks, corrosion, and wind noise
- Primer: 8 robots apply a smooth base layer that adds durability to the vehicle’s paint
- Base Paint Coat: 21 Robots (10 Painting and 11 “Opening”) paint the vehicle in up to 11 different exterior colors
- Clear Coat: The vehicle gets a clear coating to enhance the color and offers a protective coating for the paint
- Finesse & Polish: Workers identify and remove any imperfections in the paint, to ensure a smooth and flawless paint finish
General Assembly:
After the painting process is complete, the body is sent to the general assembly portion of the facility. Originally, the Mack Engine I plant, which built the Pentastar V6 engine family until December of 2019, the 1,000,000 square foot building now houses three stages of the assembly process (Trim, Chassis, and Final).
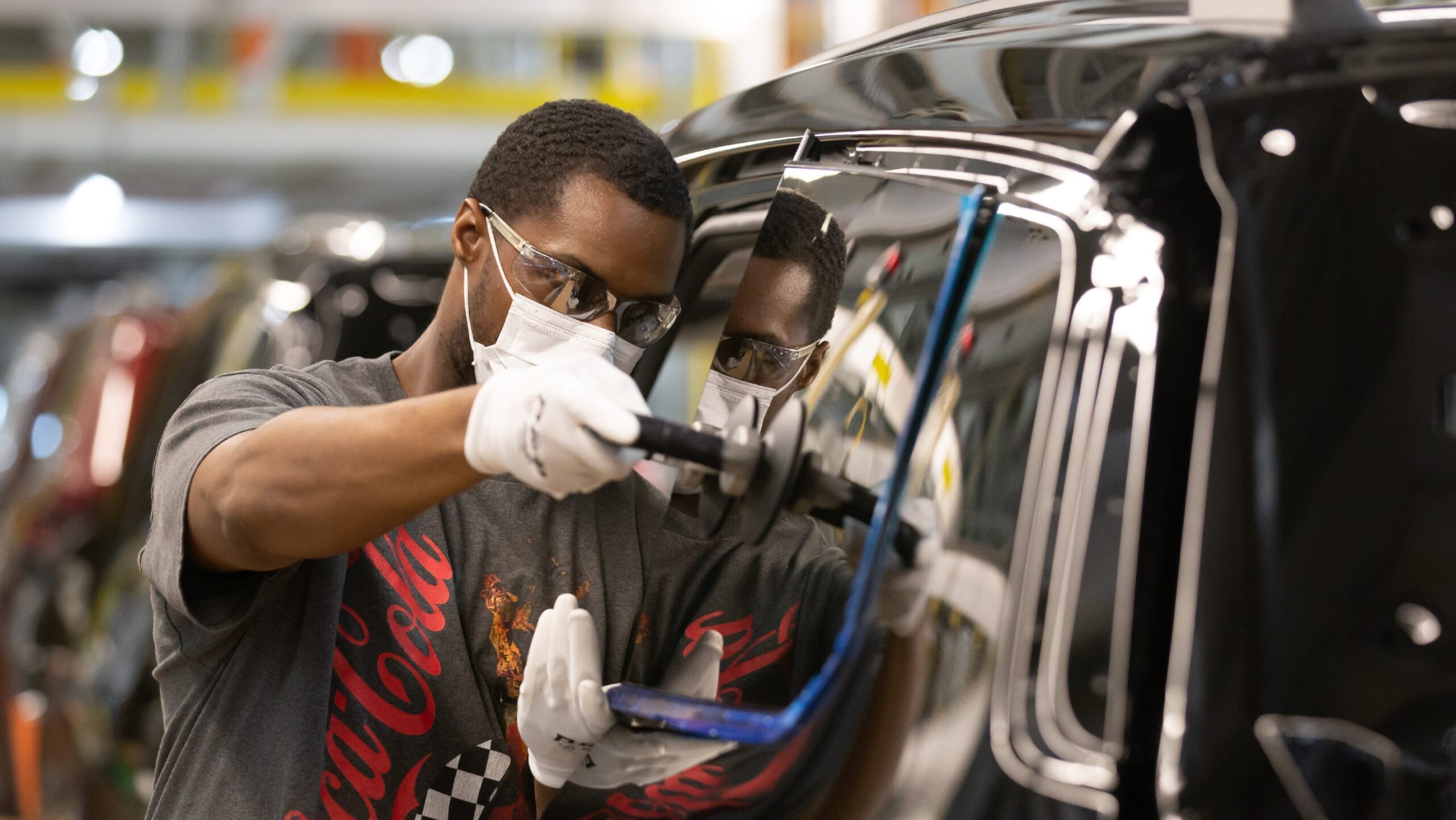
In the trim area, Grand Cherokee models receive things like the sunroof, wiring harnesses, major electrical components, instrument panel, windshield, as well as rear and half glass.
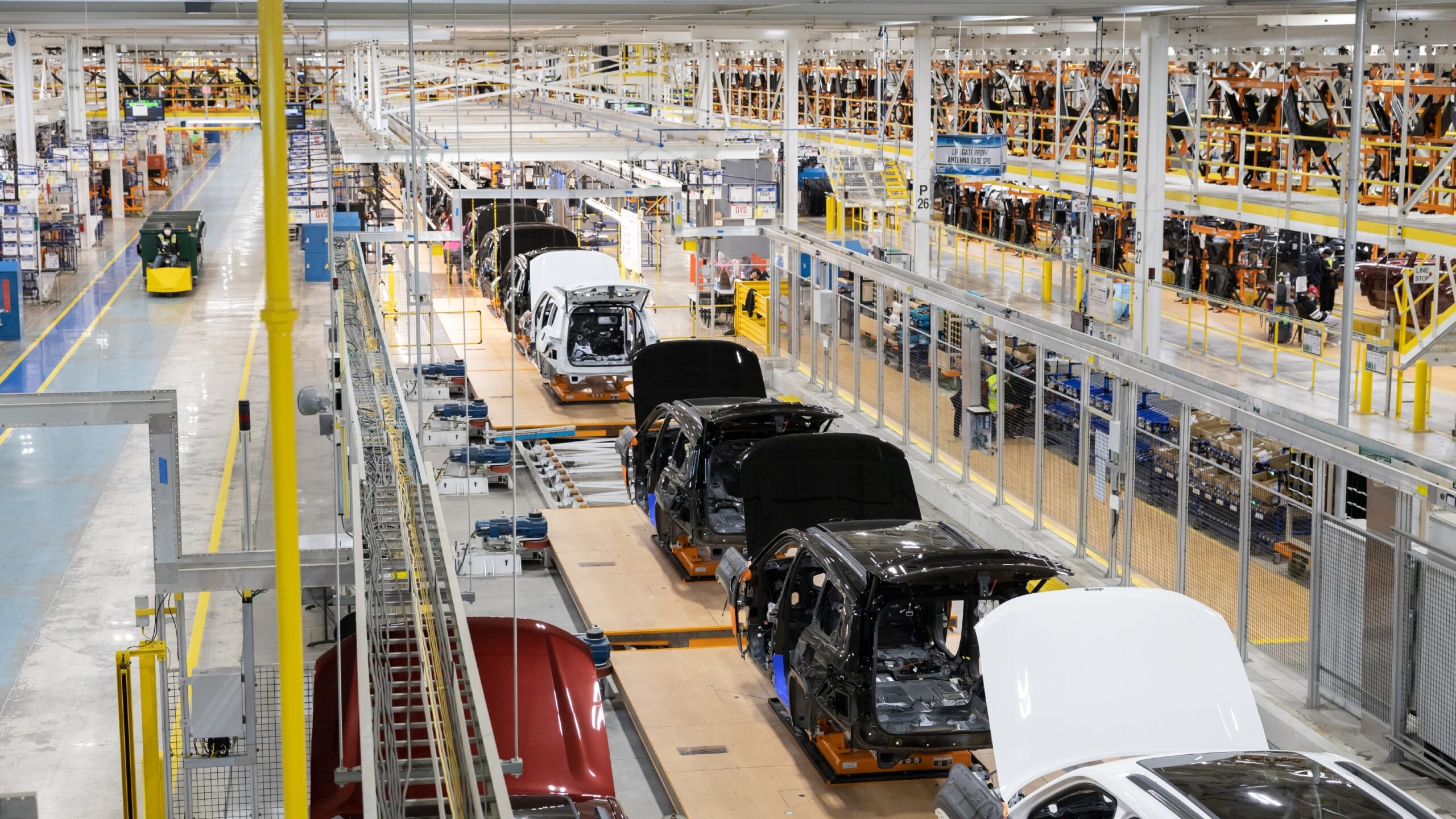
The chassis area performs engine dressing, engine and chassis marriage, body and chassis decking, hose and electrical connections, as well as filling all necessary fluids, and functionality testing.
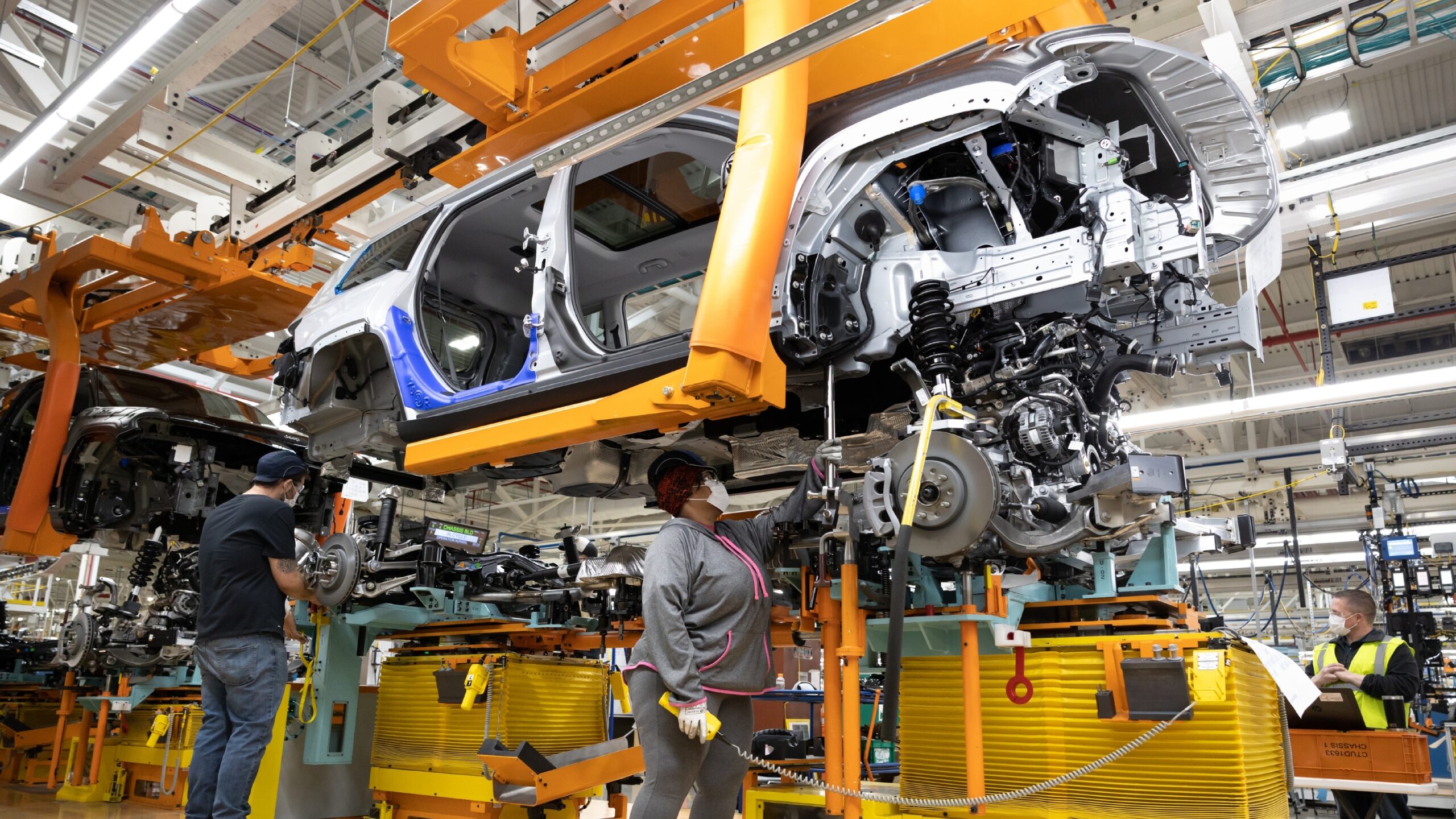
In the final assembly area, Grand Cherokees then receive their steering wheel, major components like doors, wheels, and tires, and electrical testing. After the final assembly area, conducts various checks like alignments, headlight aim, rolls, Automated Driver Assist System (ADAS) checks, before hitting the Buzz, Squeak, and Rattle (BSR) test track and inline water testing. After all the vehicles go through the certification line to make sure that the vehicle leaves the assembly line with no flaws.
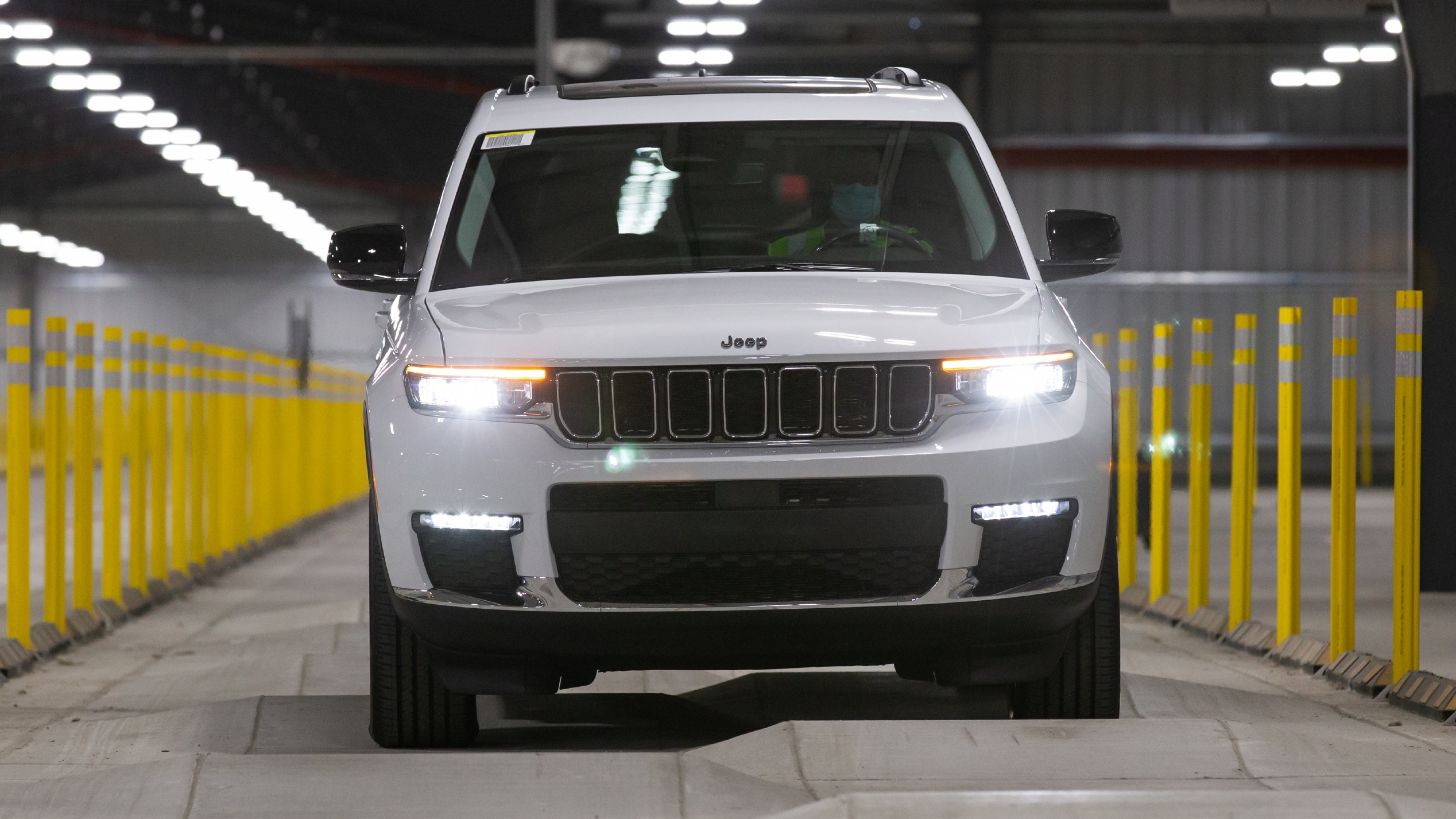
Each vehicle that is assembled at the Mack facility, is tested on the BSR test track. The test track consists of 2,000 feet of 11 different elements, which includes potholes, manhole covers, rumble strips, cobblestones, speed bumps, gravel, and a figure 8, to simulate real-world driving conditions. Each test takes about 3 minutes to conduct but insures if there are any BSRs detected, the vehicle will be fixed properly before being shipped.
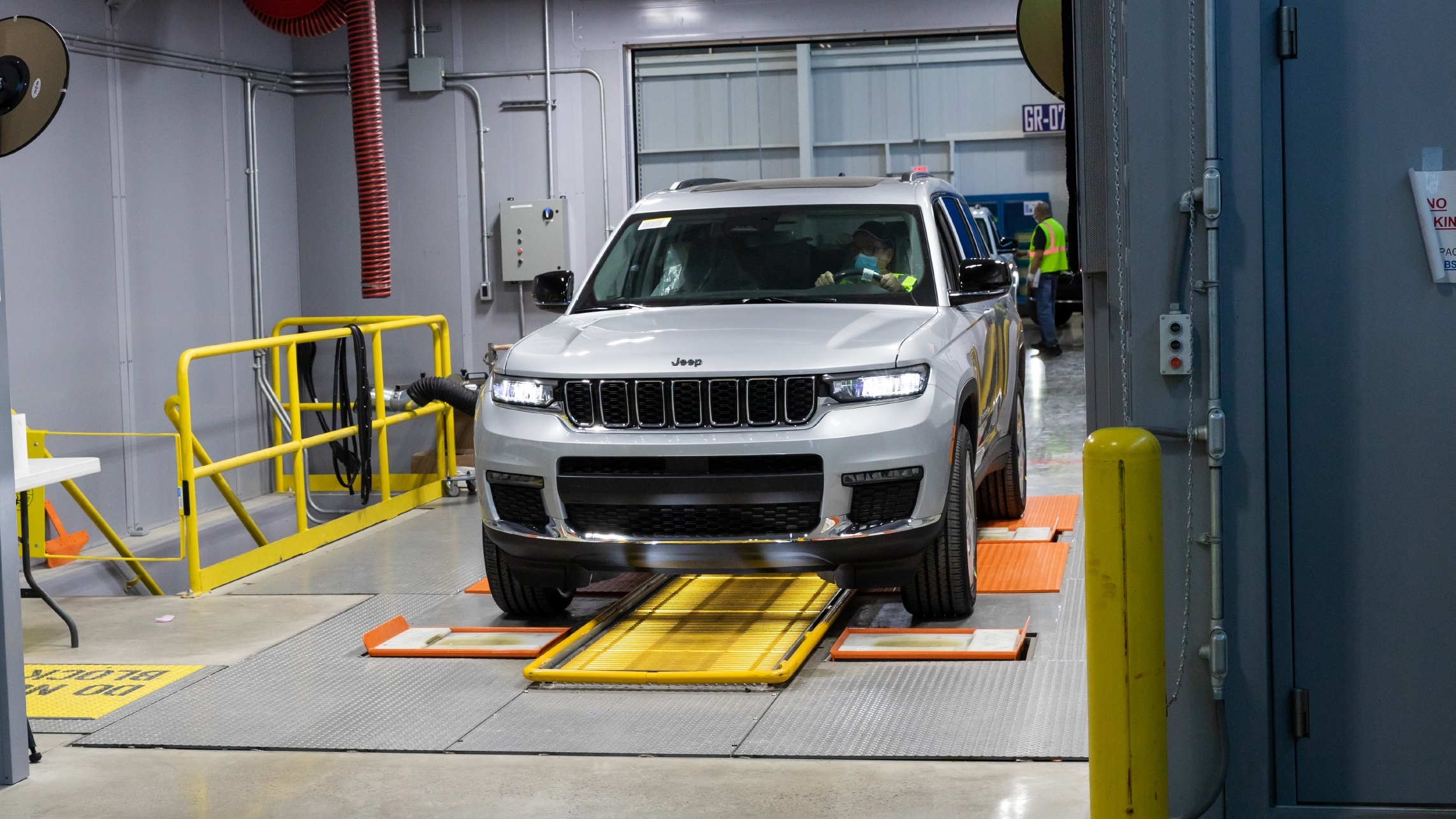
For additional validation beyond the BSR test track, vehicles can be sent to the BSR Shaker. The electro servo shaker is the first of its kind in North America and replicates the BSR test track in 2 minutes and 40 seconds, as well as additional testing like a pre-programmed profile of the more aggressive test roads at Stellantis Chelsea Proving Grounds in a 3 to 5-minute cycle, to make sure the vehicle is ready optimum customer’s satisfaction.
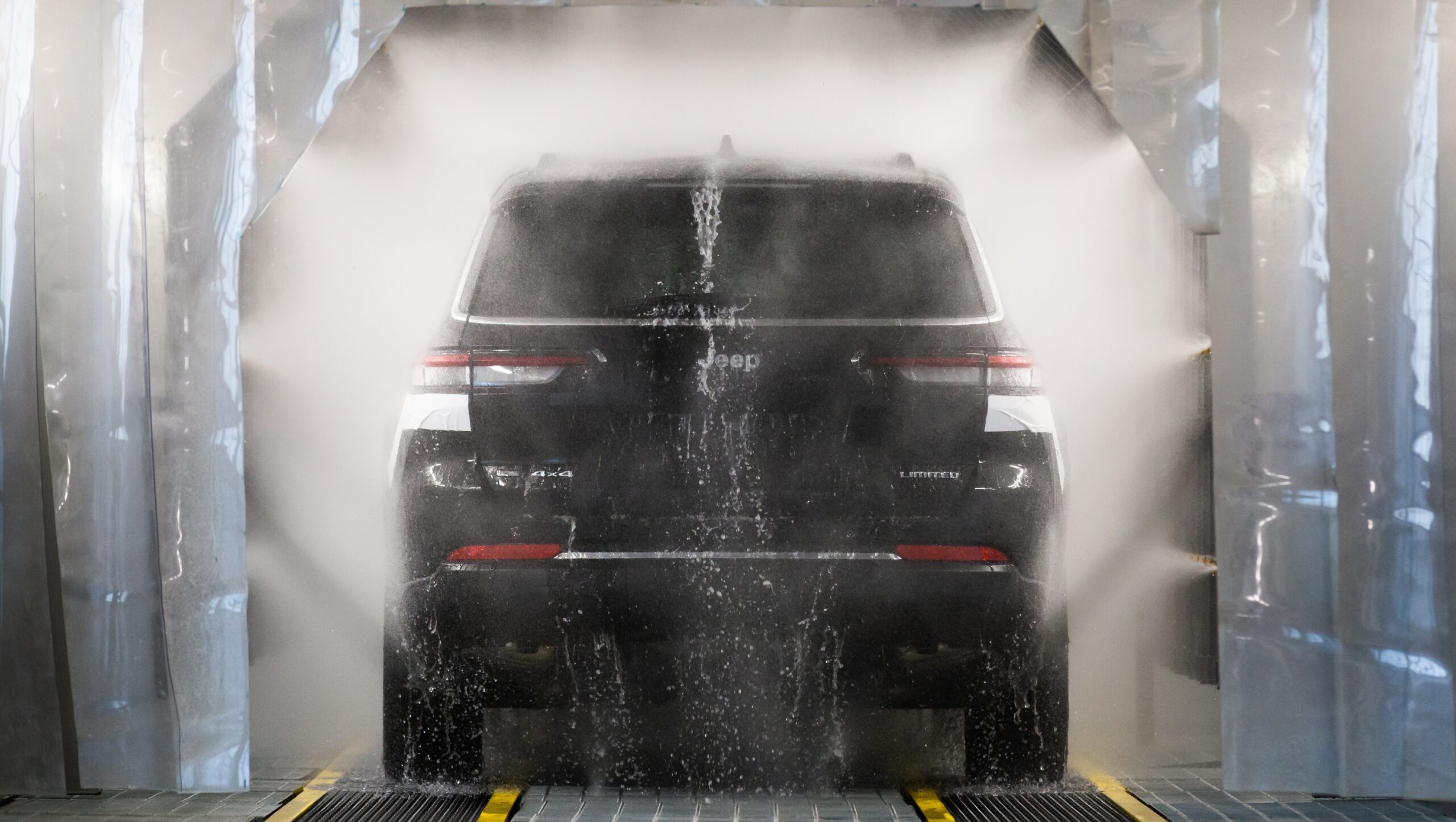
Every vehicle then goes through an inline water test, which takes 3 minutes to complete. The water test consists of 600 nozzles delivering water at 30 psi. Each vehicle is then checked for leaks before being signed off for final inspection. Vehicles can face additional validation performance in a Nine Position Water Test to simulate different terrain (hills and inclines) as well as other weather conditions.
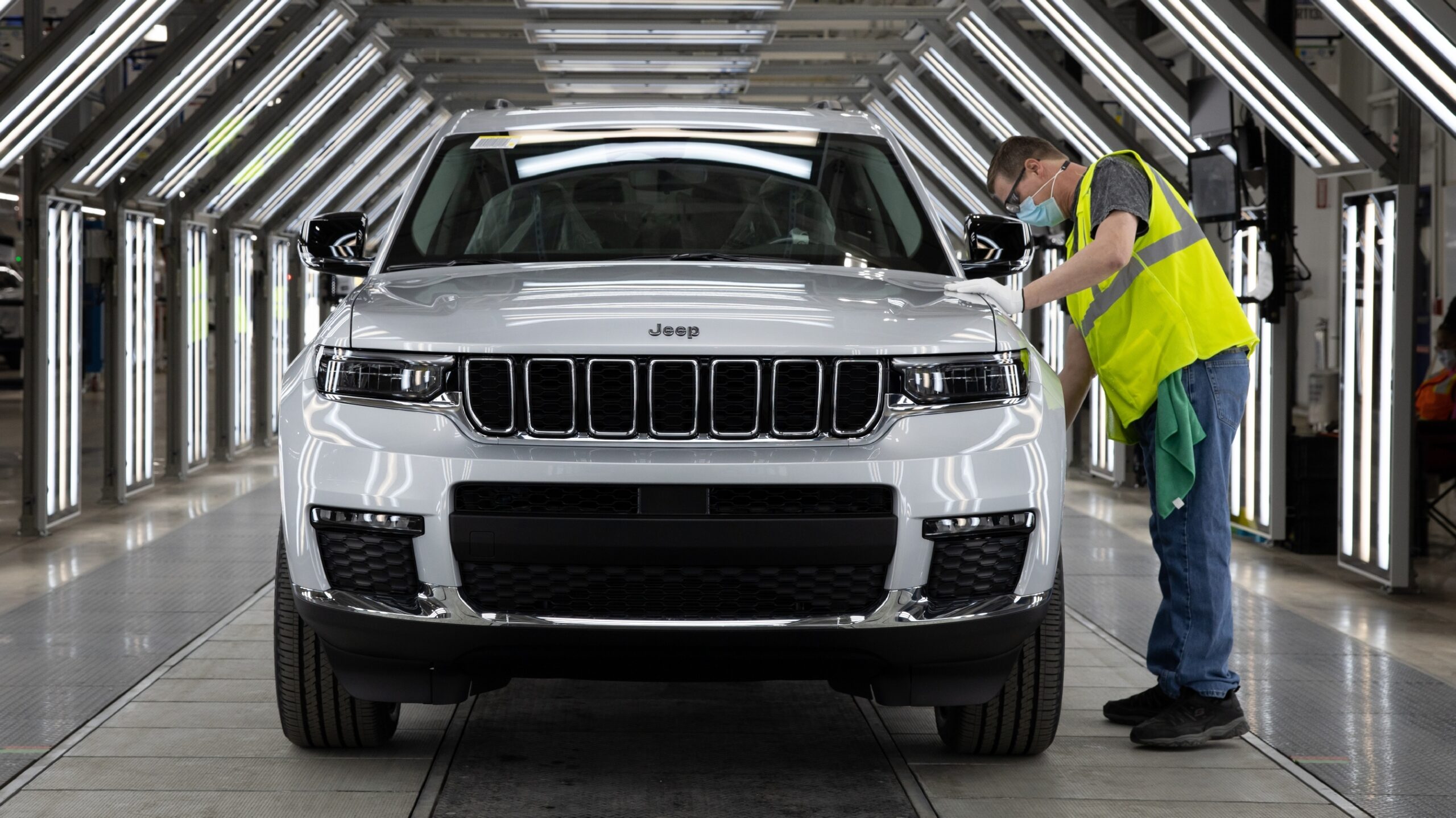
After going through the certification line, each vehicle is then ready for shipping to a Jeep dealer.
To keep up with everything surrounding the all-new fifth-generation Grand Cherokee, be sure to join our new WLJeepForum.com.
3 replies
Loading new replies...
Join the full discussion at the Mopar Insiders Forum →