How Stellantis Is Using VR to Revolutionize Car Manufacturing
Inside the Virtual Lab Transforming the Way Vehicles are Built
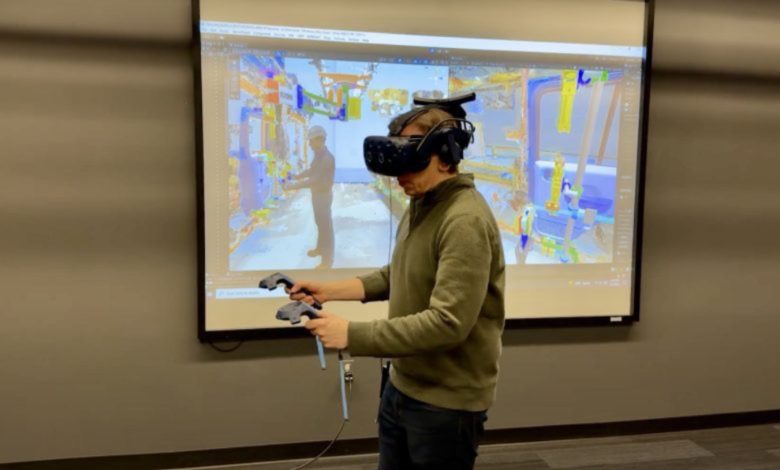
Tucked beneath the Chrysler Technology Center (CTC) in Auburn Hills, Michigan, a quiet revolution is taking place—one built not with wrenches, but with virtual reality headsets and motion-tracking sensors. Stellantis has been leveraging cutting-edge VR tech in a dedicated lab since 2018, changing the way cars and trucks are assembled before they even hit the production line.
This 40 x 42-foot VR lab, which includes a full 20 x 24-foot immersive virtual space, is helping engineers, designers, and manufacturing experts find and fix problems before a single bolt is tightened on the factory floor. Think of it as a dress rehearsal for building a car—only in a fully simulated environment where workers can walk around and interact with a digital version of the vehicle.

Borrowing techniques from the world of video games, Hollywood blockbusters, and even architecture, Stellantis is using real-time physics, motion capture, and 3D scanning to improve everything from worker posture to conveyor belt placement. The results are safer working conditions, smarter assembly processes, and better-built vehicles.
Tim Fallon, Senior Vice President and Head of North American Manufacturing, summarized: “Manufacturing is at the heart of what we do, and advanced technologies like virtual reality allow us to continuously raise the bar.”
One of the most useful tools in the lab? The ability to evaluate how hundreds of real workers move and reach while performing tasks. This helps teams figure out the best height for platforms, the most comfortable positions for hands-on assembly work, and the ideal placement for tools and parts, before construction of the factory line even begins.
For example, engineers used VR at the Sterling Heights Assembly Plant (SHAP) and Warren Truck Assembly Plant (WTAP) to simulate the best way to install underbody wiring. By testing various line heights digitally, they found the “just right” position that prevents back strain while keeping workers efficient.

The lab isn’t just about visualization either. It also includes 3D printing stations for quickly prototyping new parts. This means ideas can be tested in the real world within hours, not weeks, cutting down on waste and speeding up design tweaks.
Looking ahead, Stellantis is rolling this technology out worldwide, using the same VR strategies to help plants worldwide improve safety, minimize downtime, and boost quality.
No replies yet
Loading new replies...
Join the full discussion at the Mopar Insiders Forum →