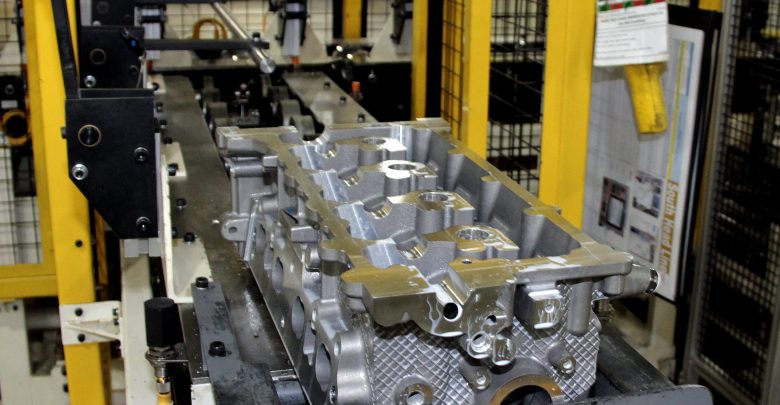
ACMZ grade alloy is stronger and withstands higher temperatures
FCA has announced that they have been working on creating a new aluminum alloy in a co-operative effort with Nemak an OEM casting supplier and the Oak Ridge National Laboratory. As the industry shifts to small displacement turbocharged engines to meet stringent fuel economy and emissions, targets a limiting factor is becoming the strength of a typical aluminum cylinder head. Today aluminum cylinder heads are generally cast from a 319 or 356 grade aluminum alloy which loses a lot if its strength above 200 degrees Celsius (392 degrees Fahrenheit).
FCAs powertrain engineers have an eye on the future and say to deliver even better efficiency without losing performance will require running higher boost pressures combined with higher compression ratios. The downside of this combination is higher temperatures in the combustion chamber (a part of the cylinder head) caused this the new ACMZ aluminum alloy grade to be born. The newly developed ACMZ aluminum alloy is capable of staying strong up to temperatures of 300 degrees Celsius (572 degrees Fahrenheit), costs only 7% more than todays alloys and is able to be cast and machined using existing technologies, all important goals that were set for the project.
Another benefit of the new alloy is the possibility that engineers may be able to reduce the size of the bridge areas of the cylinder head allowing for the use of a second spark plug or larger valves. This gives engineers the opportunity to fine tune a balance of performance and efficiency.
ACMZ aluminum alloy was created by using copper as opposed to silicon as a strengthening agent. Using copper in an aluminum alloy has been done before but the other copper infused grades are cost prohibitive, produced in small volumes and have a tendency to develop cracks during solidification. Using Oak Ridge National Laboratory’s in house Titan supercomputer engineers were able to virtually create different combinations and simulate their performance and cooling attributes before creating them in the real world.
Since this alloy was developed under a government sponsorship through the Oak Ridge National Laboratory which is federally funded, other companies will be able to use the alloy as well. FCA being involved in the development of the new alloy will give them a head start as they now have experience working with the new material. FCA, Nemak and Oak Ridge have filed for 4 different patents related to the new material.
Last edited: